This edition of the Vulcan Steel Structures e-newsletter contains:
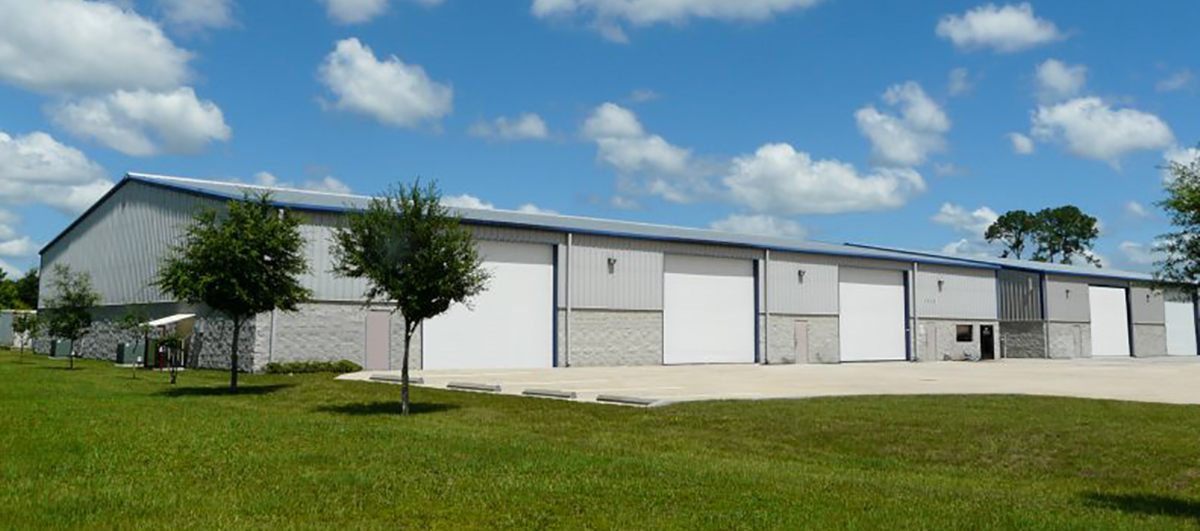
Welcome from the President
Welcome back!
This month, we’re taking a look at one of the largest buildings Vulcan has ever manufactured—the new Engineered Absorbent Materials Corporation plant in Jesup, Georgia. The main structure covers 180,000 square feet! As a point of comparison, that covers more than three football fields in total area!
We will also profile the new John Clay Automotive facility in Nicholasville, located at the heart of the state’s famed Bluegrass region. This family-owned service center has become so popular that it needed to find a larger space. We are proud to have provided the great-looking structure for their new home.
And finally, architects, designers and potential buyers are regularly inquiring about the sustainable aspects of Vulcan buildings. As part of the Metal Building Manufacturers Association (MBMA), we are pleased to provide three environmental product declarations, or EPDs, to anyone interested in the environmental impacts of metal buildings. These EPDs not only provide excellent information—they can help earn LEED points as well! Further details about these valuable resources, and where to find them, are shared in the Industry News section below.
Until next time,
Steve
Vulcan News: We’re Hiring
The May newsletter highlighted some of the major projects that Vulcan Steel Structures has on tap. The largest of these is Domtar Corporation’s new 202,000-square-foot facility for its Engineered Absorbent Materials (EAM) subsidiary in Jesup, Georgia. This is one of the biggest projects Vulcan has ever had and is currently underway. It will take 63 trucks to deliver the metal building materials from Vulcan’s plant in Adel to the project site in Jesup, which is a little over two hours away.
The main building will be 300 feet wide by 600 feet long and stand 42 feet tall at its gable ridge. It will include a 22-gauge Galvalume SL 216 standing seam roof, 26-gauge Kynar PBR walls and 26-gauge standard color PBR full-height liner panels. In addition to the main building, Vulcan is providing three lean-to structures as well as two smaller buildings.
Domtar’s EAM facility has been developing and manufacturing innovative, high-quality absorbent core solutions for the hygiene industry since 1998. This expansion project will add a large-scale airlaid production line to the facility. The new Dan-Web machine will be fully operational in 2022.
Featured Project: John Clay Automotive
This month’s spotlighted project is the new John Clay Automotive service center in Nicholasville, Kentucky. John Clay Automotive is central Kentucky’s largest privately owned, full-service auto care shop and is located just south of Lexington in the Bluegrass region of the state. The business has become so popular that it needed a new, larger facility and Vulcan was able to provide the building to make it happen.
The new metal building from Vulcan is a 9,000-square-foot clearspan structure with seven service bays and a spacious customer service area. The metal walls and roof are both from Vulcan and consist of gray PBR wall panels with blue accents and a blue standing seam metal roof.
Industry News: Steel Sustainability
The primary material used in a metal building is steel, the most recycled material in the world according to the World Steel Association. But how does that information help designers and building owners who want or need to quantify the sustainability of their facilities? Fortunately, the Metal Building Manufacturers Association (MBMA), of which Vulcan is a member, has released revised environmental product declarations (EPDs) for three metal building product categories: primary rigid framing, secondary framing, and metal cladding for roofs and walls. They are available on the MBMA website at www.mbma.com/Environmental_Product_Declarations.html.
MBMA partnered with UL Environment to develop and certify these EPDs, which summarize the cradle-to-gate environmental impacts of a metal building system. The cradle-to-gate method is used to describe the impact of producing products, from raw material extraction, through processing, fabrication and up to the finished product leaving the manufacturing facility.
EPDs are based on Product Category Rules (PCRs) used to develop a life cycle assessment (LCA) final report, which is summarized in the EPDs. The MBMA LCA was recently updated in partnership with the Athena Sustainable Materials Institute. The U.S. Green Building Council LEED version 4.1 green building rating system encourages the use of EPDs, which can be used to earn credits in the program. Both the EPDs and the LCA report are available at https://www.mbma.com/Environmental_Performance.html.